Adherents of a sporty driving style from the general flow of vehicles are distinguished by the characteristic tuning of the car, unthinkable without a direct-flow exhaust system. Although there are often more modest fans of such aggression on the roads, who do not bother with full-fledged forcing of the engine and are limited only to increasing the decibels issued by the muffler.
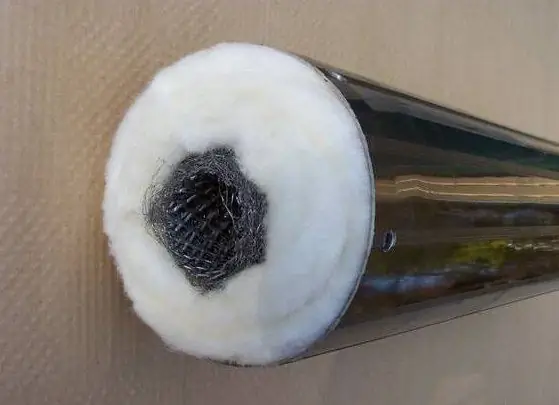
It is necessary
- - a piece of stainless pipe with a diameter of 100-700 mm,
- - a piece of stainless pipe with a diameter of 60-400 mm,
- - flanges with a diameter of 100 mm with a hole of 60 mm - 2 pcs,
- - mesh made of heat-resistant steel 600X680 mm,
- - mineral insulation 600X700 mm.
Instructions
Step 1
A straight-through muffler can be easily purchased at any car dealership. Such tuning accessories are in high demand among young drivers who dream of prohibitive speeds while driving. But a real athlete, as a rule, leads an ascetic lifestyle and does not tolerate bragging, so he will never undertake the installation of consumer goods intended for boys. And he will not be able to bribe the stickers of famous brands and the emasculated design of the product, because you can only trust in sports tuning what is done with your own hands.
Step 2
So, if you decide to join the world of sports for real men, then it's time to start with the simplest thing - with the manufacture of a direct-flow muffler for your car, which, with moderate driving, makes a noise that is no different from budget counterparts, but after overcoming 3000 rpm by the engine it begins to manifest itself with the characteristic roar of the engine.
Step 3
At the beginning, a piece of pipe with a diameter of 60 mm is cut into two equal parts. A flange is welded to one of them in the middle - this will be the inlet pipe. We leave the outer part unchanged for now, and in the half that will be inside the muffler, many holes are drilled with an electric drill with a drill with a diameter of 5-6 mm. Then the flange with the tip is welded into a pipe with a diameter of 100 mm, sinking it inward by 10 mm.
Step 4
Next, we prepare the second muffler pipe: we weld a flange at a distance of 80 mm from the edge to the remaining piece of pipe with a diameter of 60 mm - this part will later be inserted into the future muffler.
Step 5
Now, inside the pipe with a diameter of 100 mm, it is necessary to place a mineral wool insulation, which also copes well with noise reduction. To facilitate the task of filling the muffler, cotton wool is rolled along the pipe diameter and pushed through until it reaches the flange on the opposite side.
Step 6
The mesh is rolled up and lowered inside the inserted insulation, but so that it fits inside the muffler on a pipe with drilled holes.
Step 7
After the muffler is filled with a heat-noise insulator and a mesh, a pre-prepared flange with a pipe is inserted into it with a short end inside, which is recessed to a depth of 10 mm and welded into the pipe by electric welding.
Step 8
The fastening elements are cut from the old muffler with a "grinder", which are then transferred to the direct-flow one, and are also welded by welding.