A rear axle reducer is a hypoid mechanical device where the shank, or drive gear, crosses the plane of the planetary (driven) gear, forming a torque transmission by angular transformation.
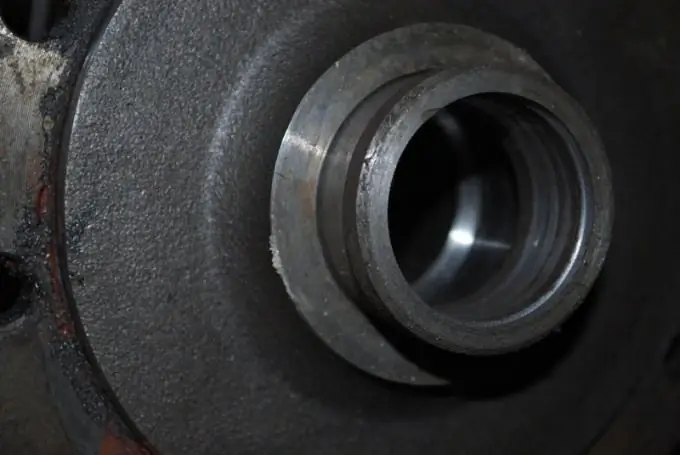
It is necessary
- - strong thread;
- - adjusting rings;
- - torque wrench;
- - fine sandpaper;.
- - vernier caliper.
Instructions
Step 1
The gearbox must be adjusted if a hum is heard at a speed of over 30 km / h. The failure of the device can be caused by long-term operation of the machine in difficult conditions, for example, constant overloading or driving with a trailer.
Step 2
Start repairing the gearbox by inspecting it. To do this, clean all parts with a brush and wash them in kerosene. If you find any defects (damage to the gear teeth), be sure to replace the damaged part.
Step 3
Pay attention to the edges between the tip of the teeth and the work surface: they must be sharp. If rounds or nicks are present, replace the main pair. Small defects can be removed with fine sandpaper and then polished.
Step 4
When assembling the gearbox, install a new flange nut, collar and spacer sleeve. If you are assembling the device in an old crankcase, calculate the change in the dimensions of the drive gear, its adjusting ring. This will tell you the difference in thickness deviation between the new and old gears. These designations are indicated by marks "-" and "+" in hundredths of a millimeter on the pinion shaft. So, if on the old gear there is the number "10", and on the new one - "-3", then the difference will be 13: 3 - (- 10) = 13. Thus, the thickness of the new adjusting ring should be 0.13 mm less than the old one.
Step 5
With a fine sandpaper, clean the seats under the bearings until they slide into place. Press the outer rings of the bearings into the crankcase. Install the inner race of the rear bearing into the crankcase using a special tool. Next, tighten the drive gear flange and the inner ring of the front bearing with a nut using a torque of 0.8-1.0 kgf.m
Step 6
Place the crankcase in a horizontal position using a spirit level. Use a flat feeler gauge to determine the gap between the fixture plate and the round rod in the bearing bed. The difference between the deflection of the new gear and the clearance will indicate the thickness of the adjusting ring.
Step 7
Place the adjusting ring on the shaft with the piece of pipe used as a mandrel. Place the shaft in the crankcase. Next, install the parts in the following order: spacer sleeve, front bearing inner ring, collar and pinion flange. Using a torque wrench, tighten the nut to 12 kgf.m.
Step 8
Wind a strong thread tightly onto the neck of the flange, attaching a dynamometer to it. Thus, you will determine the moment of rotation of the pinion shaft. With new bearings, the flange turns with a force of 6-9.5 kgf. Otherwise, tighten the nut. Remember that the tightening torque should not exceed 26 kgf.m. If, when turning, the torque exceeds 9, 5 kgf, the gearbox should be disassembled and the spacer sleeve replaced.
Step 9
Place the crankcase in the differential housing with bearings. Fix the bolts on the bearing cover. If you find axial play on the axle gears, install thicker shims. The half-axle gears should be tightly fitted, but at the same time, rotate by hand. Use a 3mm steel wrench to tighten the nuts.
Step 10
Adjust the pre-tension of the differential bearings, as well as the clearance in the main pair, by eliminating the clearances in the meshing and tightening the nut of the driven gear. Use a vernier caliper to measure the distance between the covers. Tighten nut 2 as far as it will go. The gap between the covers should be 0.1 mm larger. When turning the first nut, adjust the meshing clearance (0.08-0.13 mm). When properly repaired, a slight clatter of teeth will be heard.
Step 11
Tighten both nuts while controlling the meshing play by hand. Tighten the nuts until the distance between the covers is no more than 0.2 mm. Turn the driven gear by 3 turns, probing the play of each pair of teeth in the meshing. Install the lock plates.