Many domestic car factories, everywhere passing from carburetor engines to injection engines, tried not to change the design of the block and head much. Therefore, at home, when converting a carburetor to an injector, you can do the same: purchase an injection power system and install it instead of the carburetor one.
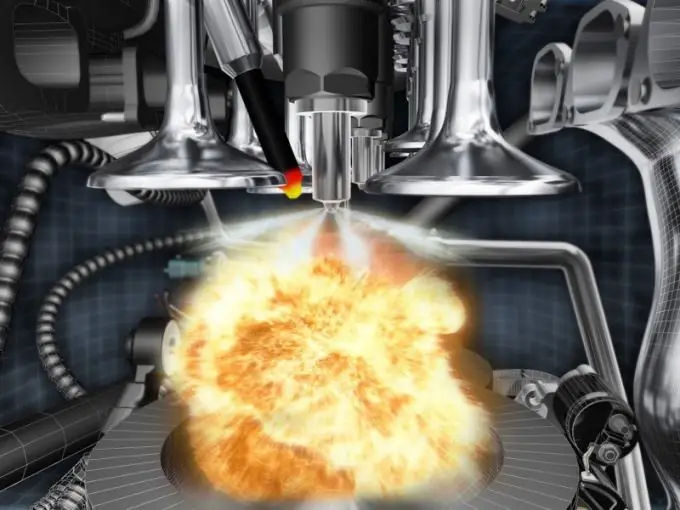
Necessary
- - complete injection system;
- - receiver;
- - intake manifold;
- - fuel line;
- - gas tank;
- - air filter housing;
- - anti-corrosion mastic;
- - gaskets;
- - new generator with pulley and belt;
- - wires.
Instructions
Step 1
Start work by choosing an injection system and purchasing the necessary parts. The cost-optimized injection system based on the BOSCH M1.5.4 controller without oxygen sensors and a neutralizer meets Russian requirements for the level of toxicity of exhaust gases. In addition, this controller offers many sports versions: there is a possibility of tuning. Assemble the power system from factory parts so as not to make changes in the design and to avoid problems when registering with the traffic police. The main parts to be purchased are: a receiver, an intake manifold, a fuel line, a gas tank, an air filter and others. It is better to purchase a complete set of attachments of the cylinder head. It will cost less than separately.
Step 2
Before disassembling the old system, flush and dry the new gas tank and install a gas pump in it. At the same time, align the arrows on the tank and the fuel pump housing and check the ease of movement of the fuel sensor float. Cover the gas tank with anti-corrosion mastic. Then drill two holes in the cylinder block, one for the knock sensor and one for the ignition module. Cut the threads inside the holes. With a close examination of the cylinder block, find ready-made holes, or special drips for them. Be careful when drilling: the depth of the hole for the knock sensor is 16 mm, for the bolt of the ignition module is 20 mm. Before operation, drain the coolant and remove the radiator and bumper. The knock sensor has a tapered thread, screw it in until it stops.
Step 3
Change the coolant outlet pipe, screw the temperature sensor into the new one. Remove the temperature sensor in the radiator (put a plug). Depending on the design, you may need a cooling tee to connect the expansion tank, as well as a gasket. Next, drain the oil, remove the sump, timing belt, toothed pulley, replace the oil pump (the new one must have a casting for mounting the position sensor KV) and the usual generator pulley with a damping with a gear ring. Change the belt to a V-belt, and also change the generator, because the injection electronics consume more energy. Don't skimp on replacing the generator. If the machine is not new, replace the oil pump and sump gaskets.
Step 4
We disassemble the power supply and ignition system. To do this, first remove the battery, then the distributor, the fuel pump with auxiliary units, the air filter with the housing, the carburetor with the manifold, the accelerator and air damper cables, the ignition wiring in the motorcycle compartment, the coil, the switch, the EPHH unit, fuel pipes, the gas tank, the vacuum hose amplifier.
Step 5
Disassemble the dashboard. Make a harness of two + 12V wires from the ignition switch terminal to the tachometer input. A separate wire for the Check Engine lamp. Apply an 8-pin connector on one side and a 4-pin connector on the other. Pull the ignition harness from the engine compartment into the passenger compartment, attach, and connect to the manufactured one. Connect the two separate wires of the injection harness (blue and blue with a black stripe) to the wiring block. In the fan relay, close the wires that used to go to the fan switch. Attach the controller, relays and fuses where provided. Add two wires connecting the fuel gauge to the fuel pump harness.
Step 6
Replace the original harness of the fuel level sensor with a new one, with a connector for the fuel pump. Put a plug on the right side of the block head, attach the "mass" of the injection harness to it. Install the manifold, fuel rail with injectors, receiver, throttle pipe. Change the throttle cable to a longer one.
Step 7
Route the fuel line under the underbody and push the return hose under the steering gear. Secure the fuel line with clamps, screw on the fuel hoses, fix the fuel filter (on the bracket to the bottom of the body). Install a new gas tank, secure it with clamps and connect the fuel line. Before installing the nozzles, check for leaks. Attach the ramp to the manifold, install separate sensors, ignition module, high-voltage wires. Fasten ground, wiring and hoses securely. Then install the air filter, the hose of the branch pipe, connect the hoses for the crankcase ventilation and heating the throttle branch pipe.
Step 8
Check the work done. A serviceable car with serviceable spare parts starts up immediately. In conclusion, connect the DST-2 and the gas analyzer, reset the errors and adjust the mixture composition at idle speed.