It seems that making a car battery charger is only for professionals. In fact, you can build such a device with your own hands, from improvised means, although this will require certain technical knowledge. To do this, you will need parts that may well be found in your home, for example, left over from an old computer.
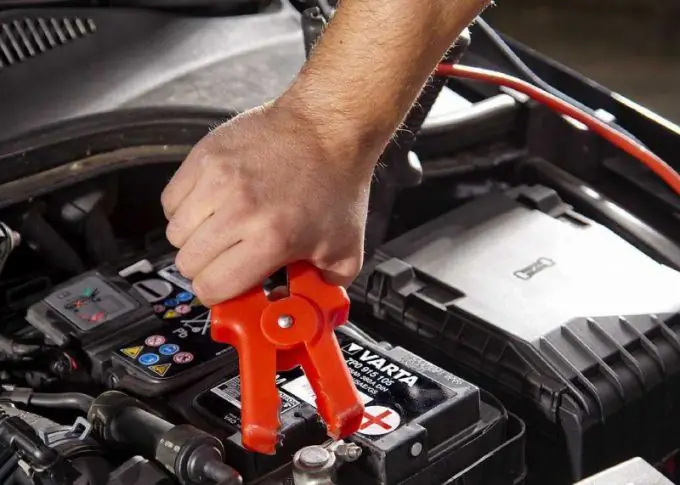
It is necessary
- • Power transformer TS-180-2, wires with a cross-section of 2.5 mm2, four diodes D242A, power plug, soldering iron, solder, fuses 0, 5A and 10A;
- • household light bulb with power up to 200 W;
- • a semiconductor diode that conducts electricity in one direction only. A laptop charger can be used as such a diode.
Instructions
Step 1
A simple car battery charger can be made from an old computer power supply. Since charging the battery requires 10% of the total battery capacity, any power supply with a capacity of more than 150 volts can be an effective source of charge. Almost all power supplies have a PWM controller based on a TL494 chip (or similar KA7500). First of all, you need to remove the extra wires (from sources -5V, -12V, + 5B, + 12B). Then remove the resistor R1 and replace it with a trimmer resistor with the highest value of 27 kOhm. The sixteenth terminal is also disconnected from the main wire, the fourteenth and fifteenth are cut at the junction.
Step 2
On the rear plate of the unit, you need to install the current regulator potentiometer R10. There are also 2 cords: one for the network, the other for the battery terminals.
Step 3
To simplify the process, it is better to prepare a resistor block in advance. It can also be made by hand: connect a pair of 5 volt current sense resistors. The total power will be 10 volts and the resistance will be 0.1 ohm. The charger must be configured for the same board. To do this, a trimming resistor is attached to it. To remove the possibility of unnecessary connections between the frame and the main circuit, it is important to remove part of the printed track. This is important because, firstly, the metal case of the power supply unit should not enter into galvanic connection with the battery charging circuit, and, secondly, a parasitic circuit is excluded.
Step 4
Now we need to deal with pins 1, 14, 15 and 16. First, they need to be irradiated. To do this, the wire is cleaned of insulation and burned with a soldering iron. This will remove the oxide film, after which the wire is applied to the piece of rosin, and then pressed again with a soldering iron. The wire should turn yellow-brown. Now you need to attach it to a piece of solder and press it for the third, last time with a soldering iron. The wire should turn silver. After the end of this procedure, it remains to solder the multi-stranded thin wires.
Step 5
Idling must be set with a variable resistor at the middle position of the potentiometer R10. The open circuit voltage will set a full charge in the range of 13.8 to 14.2 volts. Clamps are installed on the ends of the terminals. It is better to make the insulating tubes multi-colored so as not to get tangled in the wires. This can damage the device. Red usually refers to plus and black to minus.
Step 6
If the device will only be used to charge the battery, you can do without a voltmeter and ammeter. It will be enough to use the calibrated scale of the potentiometer R10 with a value of 5, 5-6, 5 amperes. The charging process from such a device should be easy, automatic and not require your additional efforts. This charger virtually eliminates the possibility of overheating or overcharging the battery.
Step 7
Another method of making a car battery with your own hands is based on using an adapted twelve-volt adapter. It does not require a car battery charger circuit. It is important to remember that the voltage of the battery and the voltage of the power supply must be equal, otherwise the charger will be useless.
Step 8
First you need to cut and strip the end of the adapter wire to 5 cm. Then the opposite wires are divorced by 40 cm. Now you need to put on a crocodile clip on each of the wires. Be sure to bring the colored clips to avoid reversing the polarity. It is necessary to consistently connect each terminal to the battery, following the principle "from plus to plus" and "from minus to minus". Now it remains to turn on the adapter. This method is quite simple, the only difficulty is in choosing the right power source. Such a battery can overheat during charging, so it is important to monitor it and interrupt it for a while in case of overheating.
Step 9
A car battery charger can be made from a regular light bulb and a diode. Such a device will be very simple and requires very few initial elements: a light bulb, a semiconductor diode, wires with terminals and a plug. The light bulb must be up to 200 volts. The higher its power, the faster the charging process will be. A semiconductor diode should only conduct electricity in one direction. You can take, for example, charging from a laptop.
Step 10
The light bulb should be lit at half the incandescence, but if it does not light at all, the circuit needs to be modified. It is possible that the light will turn off when the car battery is fully charged, but this is unlikely. Charging with such a device will take about 10 hours. Then it is imperative to disconnect it from the network, otherwise overheating is inevitable, which will disable the battery.
Step 11
If the situation is urgent, and there is no time to build more complex chargers, you can charge the battery using a powerful diode and a heater using current from the mains. You need to connect to the network in the following sequence: diode, then heater, then battery. This method is ineffective, because it consumes a lot of electricity, and the efficiency is only 1%. Therefore, this charger is the most unreliable, but also the easiest to manufacture.
Step 12
It takes considerable effort and technical knowledge to make the simplest charger possible. It is better to always have a reliable factory charger on hand, but if necessary and with sufficient technical skills, you can do it yourself.