The idle regulator is a conventional stepper motor that has a cone-shaped spring needle in its design. When the motor mechanism is idling, the required air is filled into the motor.
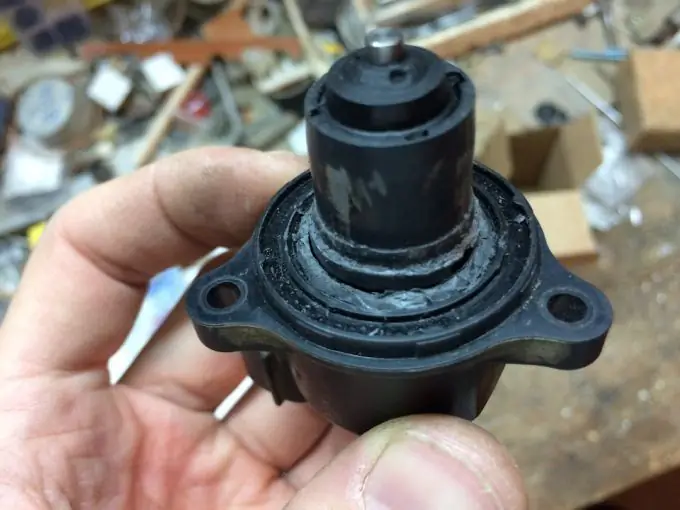
This entire process occurs together with a change in the flow area of the channel, which determines the air supply. This results in a bypass of the throttle valve, which is in the closed position.
Principle of operation
The air volume is monitored using a special sensor. The controller supplies fuel to the engine through the fuel injectors. The sensor that monitors the position of the crankshaft indicates to the controller the current engine speed. Taking into account these indicators, the considered regulator is controlled, the air supply increases or decreases.
If the engine is in a warm state, the controller maintains the required idle speed values.
Periodically, the controller on an unheated engine helps to increase the speed. The operation of the device in this way allows the machine to start moving much faster, without waiting for it to warm up. The idle regulator is fastened with a pair of screws in the throttle body. However, on some machines, the screw heads can be reamed or completely mounted on a regular screw. If it is necessary to replace the regulator or clean the air channel, this will significantly complicate the entire procedure. In such situations, the throttle body must be removed.
Since the regulator belongs to the category of executive devices, its independent diagnostics is impossible. Therefore, when this module malfunctions, the “Check Engine” inscription will not be displayed.
Malfunction symptoms
A faulty regulator may be indicated by the following symptoms:
- there is a spontaneous change in engine speed;
- increased revolutions are absent during the start of a cold engine;
- during idling, the revolutions become unstable;
- when the transmission is turned off, the engine stops;
- when the stove or headlights are turned on, the revolutions begin to decrease.
Before dismantling the regulator, disconnect its four-pin connector and loosen the two fixing screws.
The work connected with the installation of this module should be carried out in completely reverse order. It is important to ensure that the distance between the flange and the taper needle is 23 mm. You also need to pay attention to the flange and lubricate the O-ring located on it with engine oil