Compression rate, clutch wear, brake efficiency
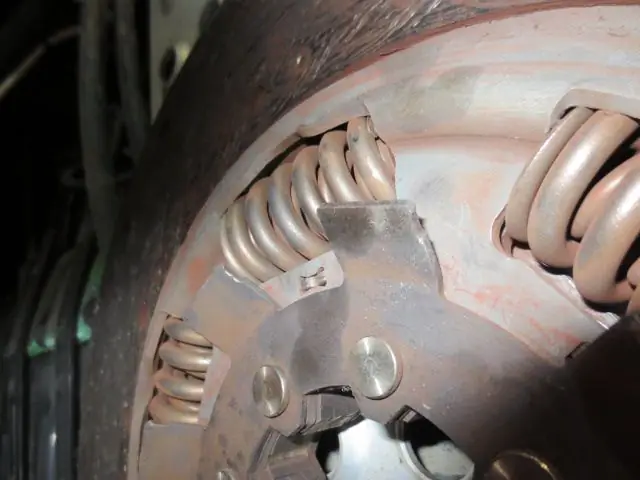
Only true up to a point. The growth in efficiency and power is not linear. It makes no sense to raise the compression ratio above 14 for reasons of increasing efficiency. How about diesel you ask. The high compression ratio of the diesel engine is also due to its starting properties. For example, an increase from 10 to 14 gives an increase in efficiency of 7%, and from 14 to 17 only 1%. However, there are diesel engines with a compression ratio of 10, which are quite economical. For example, ships with a cylinder diameter of one meter.
This is only true for baskets with radially arranged coil springs. For them, the developed force decreases linearly as the driven disk wears out. A completely different picture for a basket with a diaphragm spring. The compression force of such a spring increases linearly up to a certain moment, followed by a certain inflection point and a linear decrease in the compression force. It is this property that is used to work in the clutch basket. Accordingly, as the disc wears out, it is clamped harder and harder. But do not expect that by wearing the friction layer to the rivets, you can continue to operate the car. In this case, the effort will not be enough.
Before comparing something, it is necessary to bring it to a common denominator. How to do this with the brakes? It is possible to compare the developed braking torque only if certain conditions are met. Both the same force of activation of the mechanism, and the same shoulder of its application. It turns out that everything was invented for a long time. There is a Coefficient of Braking Efficiency, determined by the formula: K = M (torus) / (P * R) Where: M - braking torque P - sum of driving forces R - radius of application of the resulting friction force, (drum radius, average lining radius). Let's omit boring calculations. The Brake Efficiency Ratio for disc brakes will be equal to the friction coefficient of the linings. But for drum brakes, everything is not so simple, because there are the following types: - with equal driving forces and one-sided arrangement of supports; - with equal driving forces and spaced supports; - with equal displacements of the pads; - with self-reinforcement. Remember that it is in the drum brake that the shoe can be additionally pressed by frictional force, increasing the braking torque. Such a block is called active (with the opposite effect, respectively passive). It depends on the direction of travel, of course. What we see is that we have an additional downforce, the higher the higher the friction coefficient of the pad. Accordingly, a drum mechanism with two active pads will be more efficient than a disc mechanism. Ceteris paribus. But the developed braking torque will decrease much more sharply with a decrease in the coefficient of friction (wet pads, for example) on drum brakes. The additional pressing force is the less, the lower the friction force.