The stability control system or the stability control system is one of the auxiliary systems of the car that helps prevent skids and drifts when driving in bends. It is now mandatory for all new passenger cars in Europe, the USA, Canada and Australia.
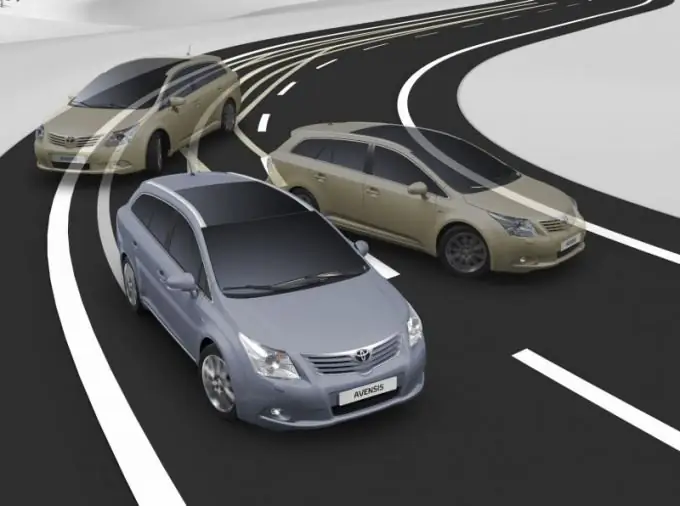
Development of stability control systems began in 1987 based on the combination of anti-lock braking systems and traction control systems. The first production car equipped with such a system was the Japanese Mitsubishi Diamante in 1990. And since 1992, BMW and Mercedes Benz cars have been equipped with stability control systems.
How the system works
If at the moment of demolition of the car one of the wheels is braked, the car can return to the previous turning trajectory, and thus a dangerous situation of loss of controllability is eliminated. As a rule, the rear wheel is braked along the inner turning radius and, at the same time, the vehicle speed is reduced using the traction control system.
In the event of a skid of the rear of the car, the stability control system brakes the front wheel running along the outer turning radius. The counter-rotating moment thus created leads to the elimination of side skid.
If the loss of control has occurred due to the slip of all four wheels, a more complex algorithm for applying the brakes is activated. Thus, the effectiveness of the system allows you to correct driver errors, preventing drifts and skids and helping to regain control of the machine. The system is capable of working at any speed and in any mode, except for cases when the travel speed is too high and the turning radius is too small. Even a perfect system is powerless against the laws of physics.
System design
As already mentioned, the system works on the basis of ABS (anti-lock braking system) sensors and a traction control system. In addition, the stability control system uses the readings of the steering position sensor, speedometer and accelerometer - a sensor that monitors the actual turn of the car.
When the steering wheel position sensor and accelerometer readings diverge, the main controller recognizes that the vehicle has lost control and entered a skid (drift). With the help of the speed sensor, the required force is calculated, which must be transmitted to the brake mechanism of one or another wheel. If necessary, the traction control system is given a command to reset the driving speed.
The main controller of the system consists of two microprocessors that read and process the sensor readings. They provide a response time of 20 milliseconds. This means that already 20 ms after the start of the drift, the system will begin to fight it. And, once it is prevented, it will shut down on its own within 20ms.
Modern exchange rate stability systems of the II and III generations combine the functions of not only anti-lock braking systems and traction control systems, but also brake force distribution systems, emergency braking assistance systems and rollover prevention systems. Off-road vehicles are equipped with hill descent and hill start assist functions.
On the latest models of Honda and Acura, the center and rear viscous couplings, which flexibly distribute the torque between the axles and the rear wheels, act in concert with the stability control system. Thanks to this, the efficiency of stabilization of movement is significantly increased, drifts and drifts are often prevented at the very beginning and the driver almost does not notice the loss of control.