The leaf spring is one of the oldest, time-tested vehicle suspension parts. At one time, the use of leaf springs was considered the only way to ensure a soft and comfortable ride. Many other suspension elements are available today, but the springs are still in use today.
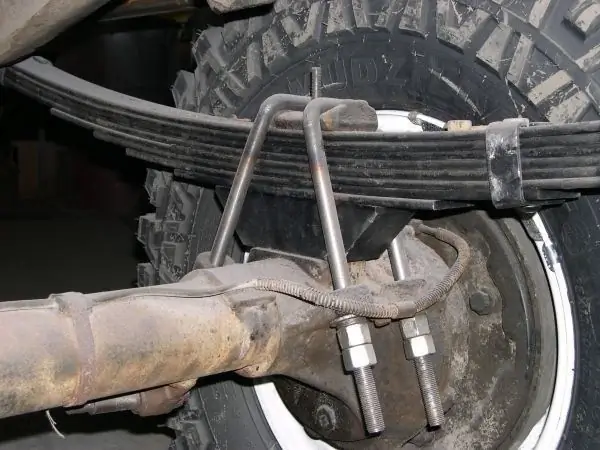
Spring is a French word that translates as "spring". This part of the modern car suspension was once widely used in the manufacture of horse carriages, in particular, carriages. Only wealthy people could afford a horse-drawn carriage on springs. Today springs are used in the design of car suspensions. The main objective of this invention is to ensure smooth running, smoothing of shocks that appear due to unevenness of the road. Such a detail not only makes the trip comfortable - this element helps to deliver the fragile cargo to its destination intact and safe, which led to the main use of the spring on trucks in the future.
How the spring ensures a smooth ride
By ride, designers mean how bouncing a vehicle is. The main factor influencing the "shaking" is the vibration frequency of the car, designed on the suspension. The frequency depends on the ratio of mass to vertical stiffness of the suspension. If the mass increases, then the spring stiffness must be greater, and vice versa. The problem with using springs in small cars is that "favorable" stiffness is achieved with increasing load (load), which can be different. Therefore, the higher it is, the more comfortable the car is. But, as statistics show, most of all a passenger car is operated with a minimum load (one driver in the cabin); therefore, springs are mainly used in the creation of trucks.
Spring design
The most common type of spring is multi-leaf. This design, which includes several sheets made of carbon steel, is considered more reliable. Such a suspension element consists of several narrow metal sheets (usually 7), tightened into a single package using a central bolt. In this case, the first sheet on top is at least 1 mm thicker than the others. The top side of each sheet is shot blasted during the manufacturing process to increase its service life.
To exclude lateral displacement of the sheets, they are additionally tightened with clamps, the number of which is at least 3. Each clamp is attached to the bottom sheet with metal rivets. From above, the ends of the clamp are pulled together with a nut, bolt or stud. The ends of the top sheet are bent in the form of lugs through which the part is attached to the car frame. Fastening is not carried out directly, but through brackets made of ductile iron. Inside the lugs of the top sheet, rubber bushings are inserted, providing a soft and at the same time reliable connection of the spring with the frame side member. The maintenance of the springs is simple and consists mainly of tightening the clamps and cleaning the sheets from dirt.