Any electric motor can be operated from an alternating current network - three-phase or single-phase. Some of them can be connected to the network directly, while others through matching elements and blocks.
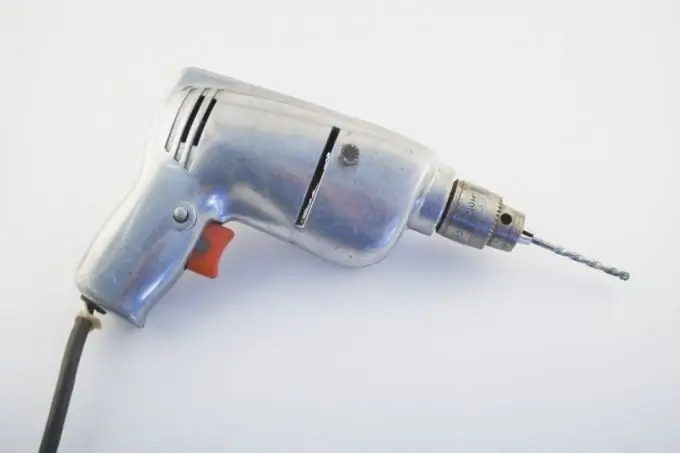
Instructions
Step 1
Collector motors with permanent magnets on the stator are available for voltages from 1.5 to 30 V. They cannot be connected directly to the network. Use a power supply that is capable of supplying a DC voltage that is rated for the motor you are using and is rated for twice the current it draws at full load. Connect a ceramic capacitor of any capacity in parallel with the motor. To reverse it, reverse the polarity of the supply voltage. Switch on the brushless motor in the same way, with the only difference that polarity must be observed, reverse is usually impossible, and the capacitor is not needed due to the absence of interference.
Step 2
Universal motors are also collector motors, but instead of permanent magnets, they have windings on the stator. They are connected in series with the collector-brush assembly. Since the voltage polarity at the stator changes synchronously with the voltage polarity at the collector-brush assembly, this type of motor can be powered with alternating voltage. If such a motor is designed for a voltage of 220 V, it can be connected directly to the network. In series with each brush, be sure to place a high-frequency choke designed for the current consumed by the motor. It is also useful to bypass the mains input (after the switch and fuse) with a metal-film capacitor with a capacity of about 0.1 μF, designed for a voltage of 630 V. The use of electrolytic capacitors, both polar and non-polar, is not allowed for this purpose. To reverse such a motor, swap the wires going to the brushes.
Step 3
A single-phase asynchronous motor cannot be reversible. If it is rated for 220 V, plug it directly into a single-phase network. Connect a two-phase motor rated for 127 V to the mains via an autotransformer with appropriate parameters. Connect its winding with a high resistance to the output of the autotransformer directly, and with a lower one through a paper capacitor, the capacity of which is indicated in the documentation. It must be rated for a voltage of 630 V. The use of electrolytic capacitors is not allowed here either. To reverse, swap the terminals of either winding, but not both at once.
Step 4
A three-phase motor, in contrast to a single-phase and two-phase, can only be connected directly to a three-phase network. If a double voltage is indicated on it - 220/380 V, the first of these numbers corresponds to inclusion with a triangle, and the second - with a star. Since a three-phase network usually has a voltage of 380 V between phases, use the second method of connecting the windings for power supply from a network with such parameters. Connect the motor housing to the grounding wire, and do not connect the zero wire anywhere. To reverse, swap any two phases. If you need to power such a motor from a single-phase network, in no case use a capacitor for this. Apply a device called a three-phase inverter. It must match the parameters of the supply network and the motor.