According to most experts, a 25-watt soldering iron is the best option for mounting resistors, which provides heating up to 3000 degrees. The fact is that excessive overheating of radio components contributes to their premature failure.
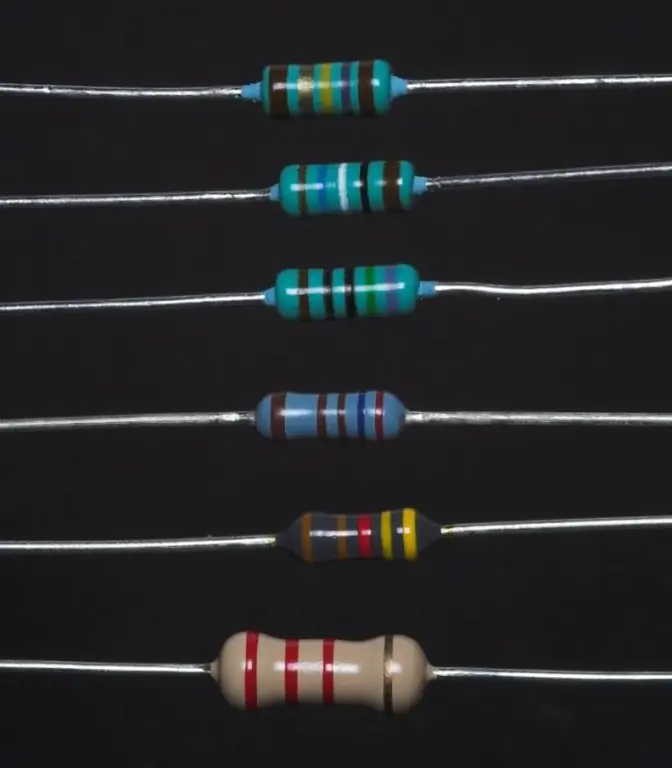
It is necessary
Soldering iron, flux, solder, wire cutters, file, tweezers
Instructions
Step 1
In addition to the soldering iron, you will need a stand, POS-61 grade solder in the form of a wire one match thick. Do not forget about the flux - a substance for degreasing and removing oxide from the work surface. By the way, you can make it yourself. To do this, you need to fill the vial with alcohol, add crushed rosin there and shake until completely dissolved. If you are working on a regular table, then to keep it safe, put a small sheet of cardboard, plywood or plexus on it. From the tool, you will probably need a small cutter, a file, tweezers and a scalpel, and from instruments - a digital tester.
Step 2
Heat the soldering iron for 15-20 minutes, immerse it in rosin and then in solder. If the part is old and the surface is covered with oxide, it must be well plated with low-melting solder.
Step 3
When using solder paste, squeeze it out into the soldering area. Before you start soldering the microcircuit, in addition to the tracks on the board, cover the legs of the microcircuit with paste, especially on the QFN. Here, grease the pins well with paste and cover them with a thin layer, while the paste should not get under the base of the QFN board.
Step 4
If you decide to solder the microcircuit to the board, where there are vias and tracks under the case, then it is better to break off the heat sink base of the case. This is done using a round or square copper rod that is one and a half times thinner than the width of the heat sink base.
Step 5
After that, lightly clamp the microcircuit in a vice, placing paper spacers under the jaws of the vice, and with careful movements of the bar break out the base. Apply the soldering iron tip to the resistor with the entire spatula. Thus, you will provide the most efficient heat dissipation and make the soldering faster and better. To prevent the flux from evaporating at the time of soldering, apply it before soldering, when everything is ready to work. Good soldering is characterized by a thin, even, shiny layer of solidified solder, without sagging and cracks.