Failure of the carburetor is a pronounced, rather long (up to 5 seconds or more) decrease in the acceleration of the car up to its slight deceleration, despite the fact that the throttle valves are fully open. The duration and degree of acceleration decrease determine the depth of the dip.
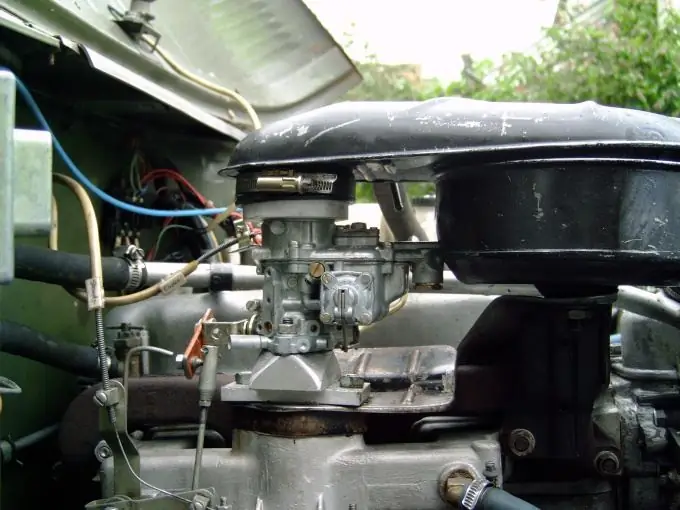
Instructions
Step 1
Before interfering with the carburetor to eliminate the failure, make sure that the fuel supply system to the carburetor is in good working order and that the ignition system is in good working order. In particular, check the clogging of the fuel intake, the fuel supply line from the tank to the carburetor, fuel filters, and the tightness of the fuel pump valves.
Step 2
In the ignition system, check the ignition timing, the tightness of the vacuum supply pipe to the vacuum regulator, the spark plugs (including the spark gap), the cleanliness of the wires, the distributor cover, the breaker contacts, the distributor slider resistor, the ignition coil
Step 3
After all the checks carried out, you can be sure that the reason for the failure lies in the carburetor. Visually inspect the appearance of the carburetor for any defects. If no defects were found, remove the carburetor and remove its cover. The fittings on the carburetor cover must be firmly seated. The strainer must be clean and free of breaks. The needle valve body must be tightly tightened onto the bonnet. The ball of the needle should be easily recessed and returned to its original position. Floats should not be jammed or distorted.
Step 4
Check the jets for clogging. The air damper should close the inlet very tightly and rotate without jamming. Its lever should not have any backlash at the attachment point. The diaphragm stem should be easy to sink and return to its original position. The needle must be sealed. The markings on the tip and orifice of the solenoid valve must correspond to the vehicle documentation. The valve itself should be screwed tightly into the cover.
Step 5
Begin inspection of the carburetor body by marking the threaded jets in the fuel wells and air emulsion tubes. Accelerator pump nozzles must have a tight fit and the O-ring must ensure proper tightness. The discharge valve ball must move freely. The axis of the accelerator pump lever must be pressed tightly, the cover screws are tightened. The resistance of the diaphragm spring should be felt as the accelerator pump lever is moved.
Step 6
When pumping fuel manually, the accelerator pump must produce even jets of fuel that do not fall on the diffusers. Any deviations in the shape and direction of the jets indicate a clogged or kinked spray. No jets indicate a defective discharge valve, a dirty spray gun, or a dirty diaphragm. Small diffusers should be fully inserted into their seats and facing the main air jets.
Step 7
The throttle shafts must not bind. The stop screw on the secondary throttle valve should provide 0.1 mm clearance at the edges of the closed throttle. This gap should not exist if the second pump sprayer is bent into the first chamber, as well as on the Niva carburetor. Clean the crankcase ventilation ducts and inlet fitting.
Step 8
The screws for the quantity and quality of the fuel mixture must be sealed with undamaged rubber rings. The cause of the failure of the carburetor may be a violation of the idle speed adjustments, which are performed by the screws for the quantity and quality of the fuel mixture. The throttle position sensor wire must be secured with two tendrils to the metal head of the throttle body screw.
Step 9
If, after diagnosing and eliminating the above malfunctions, the dips in the carburetor operation have not disappeared, adjust the fuel mixture (including idling), adjust the fuel level, adjust the float mechanism, starting device and other carburetor systems.