At first glance, there is nothing super complicated in the design of the turbine. The pressurization unit consists of 3 parts - sealing rings, compressor and bearing housing. And many motorists, with such a visible simplicity of it, want to independently repair a faulty unit. But few have the skills to remove it.
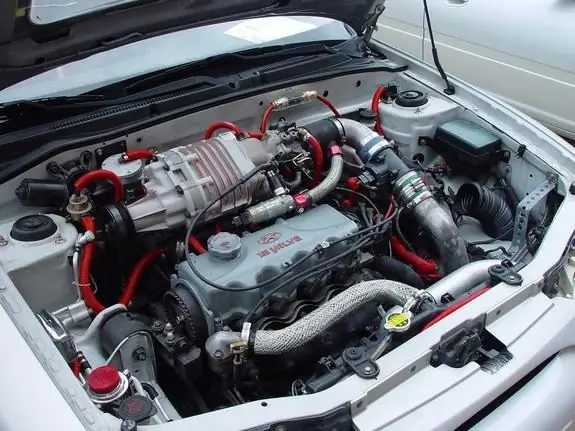
Necessary
- - screwdriver;
- - cleaver;
- - spanners.
Instructions
Step 1
Damp the rotor shaft first. This is due to the fact that the exhaust gases pass through the turbine in a discontinuous flow, impulses that hit the wheel blades in accordance with the opening-closing of the exhaust valves in the engine cylinders. The thin rotor shaft is not very rigid, and in order to compensate for such an impact on it, floating-type bushings are used in turbines. Thanks to the installation of such bearings, they will rotate together with the rotor at a lower frequency. But at the same time, the oil, which is supplied under pressure to the bearing, will already create two layers. They, like shock absorbers, will damp rotor vibrations.
Step 2
Carve new bushings out of bronze if you find a large backlash in the turbine design. Be sure to make them look like normal ones, since then they will need to be pressed into the starter or in the upper head of the connecting rod. Unscrew the nuts on the cartridge with a wrench to disassemble the bearing assembly and replace with a new one.
Step 3
After assembling the rotor, you will need to balance it, as it will inevitably acquire an imbalance during the repair of the turbine. And the loads generated by it turn out to be excessive both for the turbine itself and for its components. And if it is not balanced, it will fail very quickly. After self-repair of the structure itself, such a procedure must be performed in a car workshop using special equipment.
Step 4
Flush the oil supply pipe before proceeding with the installation of the repaired unit. This must be done to prevent dirt from entering the turbine. Then fill the oil inlet with 10-15 g of clean engine oil that you use in the engine. Turn the turbocharger rotor several times by hand. Then lead in the air ducts and with a screwdriver and fasten them carefully. Run the engine for 10 - 15 minutes, let it idle.