If a car can be painted at any service station, then chrome parts are much more difficult to restore. However, if you are familiar with physics and chemistry, and also find the necessary materials, you can repair the chrome plating yourself.
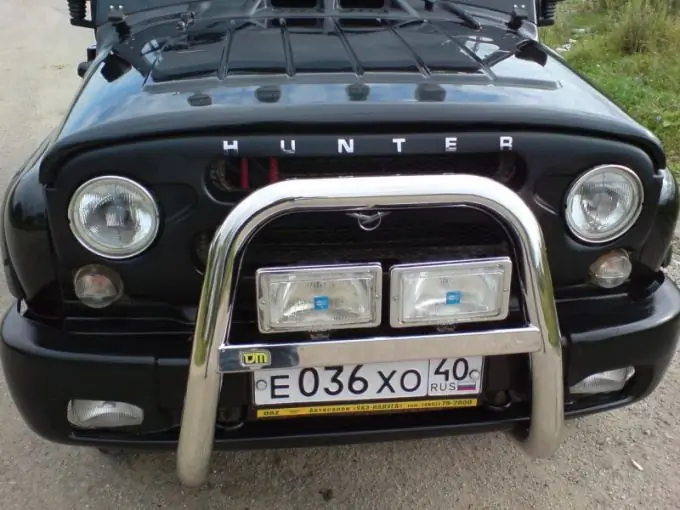
Necessary
- - Grinder;
- - gasoline or kerosene;
- - non-metallic dishes;
- - galvanic station;
- - measuring equipment (scales, thermometer);
- - chemicals and electrolytes.
Instructions
Step 1
Parts, on which it is necessary to restore the coating, process with grinding tools in order to remove all irregularities, to smooth out the risks and cavities. First sand the surface with coarse emery tips, then gradually reduce the number down to felt and felt tips. As a result, you should get a smooth, even surface.
Step 2
Degrease the surface with gasoline or kerosene. Soak the brush in liquid and clean the part from dirt, stains, rust and scale. If the part is heavily soiled, treat it in several baths filled with gasoline or kerosene.
Step 3
Wash off traces of alkali, first in hot, then in cold water. If necessary, add additional pickling to remove any remaining traces of scale or oxides.
Step 4
Pickling should be done immediately before immersing the part in the plating bath, it will help to reveal the metal structure and provide better adhesion. As a solution, take a mixture of hydrochloric (5%) and sulfuric (10%) acids, as well as water (85%). The current density should not exceed 10A / dm2. After pickling, rinse the part in warm water, being careful not to touch it with your hands.
Step 5
Copper the part with pyrophosphate or acidic electrolytes. First, pickle the product in 10% sodium pyrophosphate solution for 5-10 minutes, at room temperature. In this case, the current density should be 5-6A / dm2.
Step 6
To build up a layer after pyrophosphate or cyanide copper plating, use an electrolyte of sulfuric acid (50-75 g / liter) and copper sulfate (200 g / liter) at a current density of 1-2 A / m2. Remember to filter the electrolyte in acidic baths.
Step 7
Chrome plating the part. Connect the part with a wire connected to a negative current source, check the reliability of the contact. It is better to prepare in advance the devices with which the part will be immersed in the bath in order to ensure ease of use and minimal voltage loss.
Step 8
Use the following composition as an electrolyte: cryolite - 0.2 g / liter, chrome andigrid - 250 g / liter, sodium nitrate - 3-5 g / liter, chromine - 2-3 g / liter. Start with a current density of 25-30 A / dm2, after 1-2 minutes increase it to 20 A / dm2. In this mode, continue the process for 7-10 minutes at room temperature.