Electric motors are widely used in the subsystems of a modern car. Sometimes, if the operating rules are violated or if there are factory defects, the engine may completely fail or work intermittently. In some cases, you can repair an electric motor on your own in a home workshop. Engine repair begins with diagnosing the malfunction and identifying the cause of the breakdown.
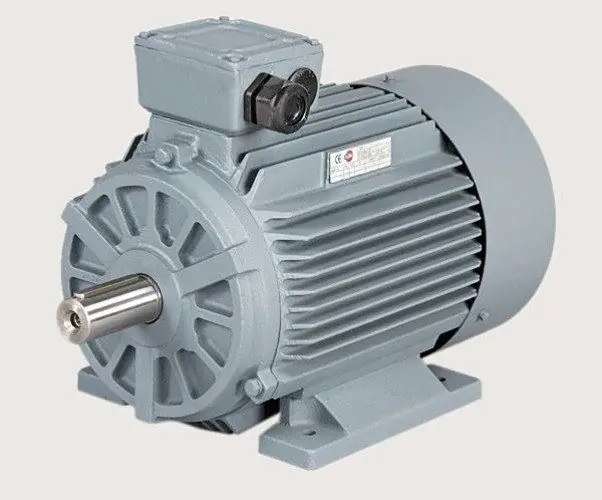
Necessary
- - a set of locksmith tools;
- - tester;
- - soldering iron;
- - insulating tape.
Instructions
Step 1
Begin your repair by checking the condition of the motor. Inspect it for external signs of malfunction. This can be deformation of the case or traces of carbon deposits on the windings. To inspect the windings, first remove the protective casing (housing) from the motor and clean the components from dust and possible contamination.
Step 2
When carrying out routine maintenance in order to prevent and improve the reliability of the unit, completely disassemble the engine with a rotor recess and a bulkhead of weakened wedges.
Step 3
Flush the plain bearings, measure the rolling bearing clearances. Replace these elements with new ones if there are face wear or cracks. Check that the bearings are properly seated on the motor shaft. Eliminate excessively large interference or, conversely, slack.
Step 4
Inspect the stator. Make sure that the steel plates are pressed firmly and the spacers are firmly attached to the channels. Heating and destruction of the winding can be caused precisely by weak pressing. Compaction steel sheets by laying mica sheets or hammering in getinax wedges.
Step 5
After completing the preventive maintenance, change the lubricant, clean the stator and rotor with the cover removed. Dry the engine with external heating. Use a blower to dry, blowing hot air through the engine openings. In the absence of a hot air source, drying can be carried out by switching on the stator winding to a reduced voltage.
Step 6
In the presence of turn-to-turn short circuits or a winding burnout, rewind it. To do this, remove the winding and insulation. Select and calculate the number of turns in accordance with the cross-section of the wire. After winding, connect the coils by soldering and wedge them in the grooves. Dry the new winding using one of the methods above.
Step 7
After completing the repair, reassemble the structural elements and check the engine for operability before reinstalling.