Any car owner wants his purchase to look original and not standard. On the other hand, choosing the right wheel rims will provide more comfortable handling, extend suspension life and reduce fuel consumption.
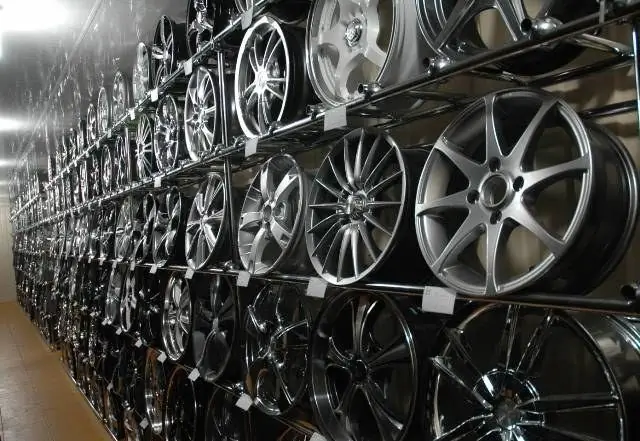
Today, motorists use three types of car disks. Each of them differs in its operational characteristics, production method, shape, design and cost. When choosing one or another wheel, it is necessary to take into account the future conditions of its operation, in particular the quality of the road surface, the purpose of the car.
Stamped
The most common type of disc (sometimes called iron). The main advantage is affordable cost. This is primarily due to the manufacturing technology: metal sheets are pressed, creating 2 parts - inner and outer, which are connected by means of spot welding. To prevent the effects of corrosion, the finished disc is coated with powder paint. The technical advantage of this type of disk is a high level of maintainability; a product crumpled on Russian bumps can be straightened in a car service. But there are more cons:
- solid mass, which leads to strenuous work of the suspension and higher fuel consumption;
- low resistance to corrosion;
- lack of uniqueness, which makes it impossible to implement original design solutions.
Cast
Cost more than stamped, at least 2-3 times. Their production involves the use of various alloys based on magnesium and aluminum. Alloy wheels weigh less stamped, plus, a huge design choice. The mechanical strength of cast disks, in comparison with stamped ones, is 15-20% higher, plasticity is 1.5-2 times better. The lower weight reduces the stress on the suspension and leads to fuel savings. However, alloy wheels require a more careful attitude towards them - you should not drive over bumps and bumpy roads, because in case of significant damage, the product may simply fall apart. Modern production technology can be in the form of:
- gravity casting: used in the manufacture of disks from aluminum alloys;
- die casting or back pressure: used for the manufacture of magnesium discs.
Wrought iron
They differ from their “colleagues” by a more complex production technology, which implies hot stamping, hardening, artificial aging and machining. The result is a fibrous structure that reduces the mass of the disc; it is 50% lighter than stamped, and 30% lighter than cast. The forged disc is able to withstand high loads and does not corrode. Of the minuses, we can note some paucity of design solutions, which is associated with the peculiarities of production, and high cost.