Correct and efficient operation of an automobile engine is possible only if all its constituent systems are in good working order. For smooth operation, a modern car is equipped with a wide variety of sensors and regulatory subsystems. One of the elements required to stabilize the engine speed is the idle speed sensor.
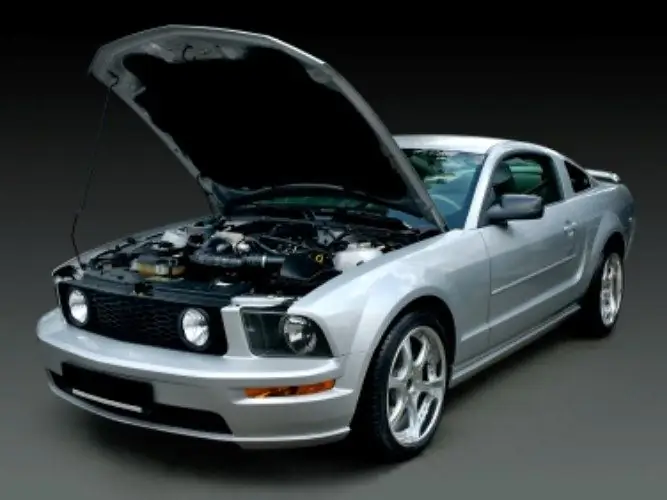
The idle speed sensor is a device that is part of the vehicle control system and performs the function of stabilizing the idle speed. This device is a tapered needle motor. Thanks to this sensor, the supply of air to the engine is ensured, which is necessary for stable operation in idle mode. This happens due to a change in the size of the section of the air supply channel.
The volume of air that has passed through the regulator is read by an air flow sensor. After that, the controller supplies the fuel mixture to the car engine through special fuel injectors. The system, which includes an idle sensor, also automatically monitors engine speed and mode of operation, increasing the flow of air bypassing the throttle valve or decreasing it.
With the engine running, warmed up to a certain temperature, the controller maintains the required idle speed. In the event that the engine is not properly warmed up, the idle speed sensor will increase rpm to warm up the engine at high crankshaft rpm. In this mode, you can, if necessary, start driving without waiting for the engine to warm up completely.
An idle speed sensor is installed on the throttle body, where it is attached with two screws. Sometimes the screws may have reamed heads or be set on varnish, making it difficult to dismantle the device for service and repair. In such cases, it is recommended not to touch the sensor mounting, but to remove the throttle valve completely.
Signs of a sensor malfunction are the instability of idle speed, dips or jumps when accelerating, stopping the engine, reducing the speed when the load is turned on. To eliminate the malfunction, disconnect the sensor connector with the ignition off, and then unscrew the fasteners. After repair or replacement, refit the instrument by checking the distance between the flange and the taper needle; it should not exceed 23 mm. As a preventive measure, lubricate the O-ring with engine oil.