Statistics show that a significant proportion of diesel engine malfunctions occur in fuel supply systems. The biggest cost is the repair of the high pressure fuel pump, which supplies fuel to the injectors. In order to reduce the risk of failure of the fuel pump, timely and correct adjustment of this device is necessary.
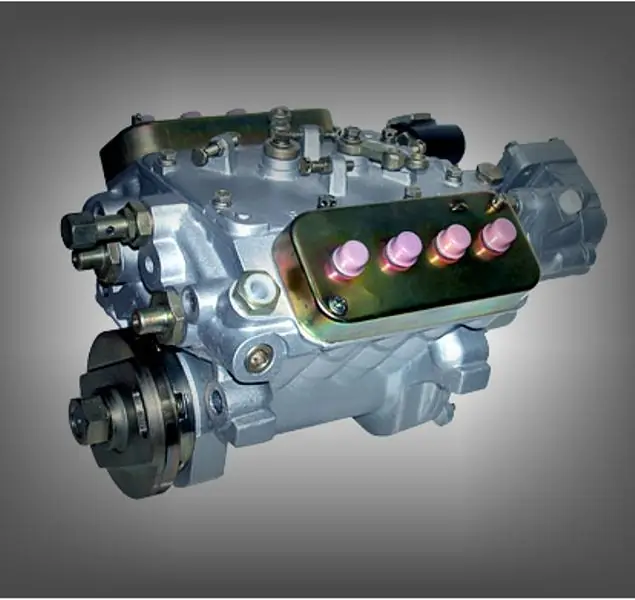
Necessary
Test stand
Instructions
Step 1
Install the fuel pump prepared for adjustment on the bench, check the oil level in the pump housing and regulator. Add oil if necessary. Rotate the drive shaft by hand to make sure it is free of binding or sticking. Remove air from the fuel system.
Step 2
Run the fuel pump in the following mode: first, without injectors, completely supplying fuel (15 minutes); then with injectors at rated speed (30 minutes). To ensure uniform fuel supply, set the clamps of the first pump element at a distance of 50 mm from the pump fender, and set the remaining clamps every 40 mm.
Step 3
When running in, check the tightness of the joints, and also check for local heating, extraneous knocks and other defects. At the end of the break-in, change the oil in the regulator and pump housing.
Step 4
Adjust the angle of the start of fuel delivery. Disconnect the low and high pressure lines from the pump. Replace the bypass valve with a process load and connect a high pressure hose to the pump head inlet. Screw flexible tubes onto the fittings of the pump sections, the free ends of which are inserted into the sockets of the stand.
Step 5
Apply high pressure fuel to the pump head and slowly turn the drive shaft with a knob. Find the angle of the start of the feed using the divisions on the graduated disc. The pump rack must be in the “flow on” position. Determine the fuel delivery angles for the rest of the sections in the same way. Compare the obtained data with the table values and adjust if necessary.
Step 6
Adjust the rail travel. Set the travel of the corrector fork so that its end protrudes above the front plane of the fork by no more than 15 mm. Measure the movement of the rack with a vernier caliper from the mating plane of the fuel pump to any rack clamp.
Step 7
Adjust the regulator. With the stand turned on, make sure there are no knocks in the regulator and pump. By changing the shaft speed, check if the weights touch the regulator body. Set the speed of the regulator by changing the number of shims under the head of the restricting bolt.
Step 8
Adjust the rated fuel supply. Turn on the stand and let it run for about 20 minutes. Perform the adjustment with the feed turned on at the rated shaft speed.
Step 9
Adjust the starting angle and alternation of fuel injection. For this, a stroboscopic device is used, the principle of operation of which is described in the manual attached to the stand.
Step 10
Now check and, if necessary, adjust the cyclic fuel supply. The difference in capacity between pump sections should not exceed 3%.