Carburetor rework is a performance modification procedure. The refinement allows solving such problems as: improving the mixture formation process, which leads to a more complete combustion of fuel; increasing the efficiency of the engine in a different range of operating modes.
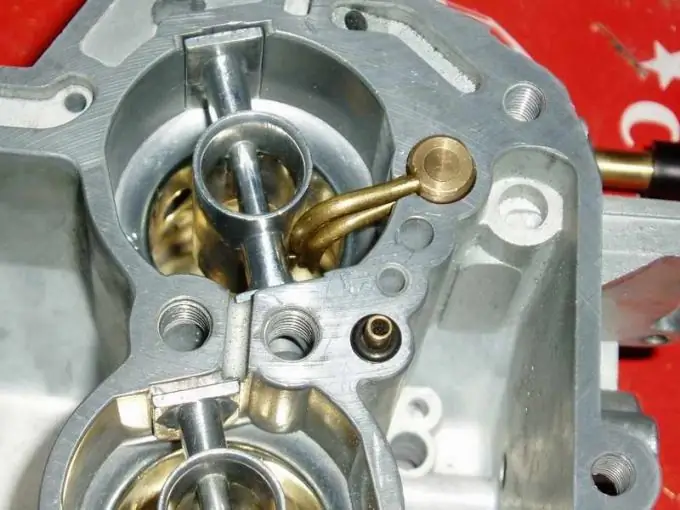
Necessary
Flat screwdriver, figured screwdriver, soldering iron, solder, soldering flux, drill, set of drills
Instructions
Step 1
An important rework unit is the needle valve of the float chamber. You need to adjust the tongue of the float so that its plane is strictly perpendicular to the needle. To do this, unbend the tongue and bend it again so that the bend is closer to the axis of the float. To avoid uneven wear and loss of valve tightness, remove the stepladder connecting the tongue and needle.
Step 2
Before modifying the accelerator pump, you need to check its operability: to do this, place the carburetor over the container and make ten strokes with the lever for opening the first chamber. Use a syringe to collect the spilled fuel, its volume should be at least 9 cubes. If this does not happen, then you need to unscrew the speed adjustment screw of the accelerating pump and, using a soldering iron, solder a small amount of tin onto the tip of the screw. Process the soldered piece so that you get a cone to start with a length of no more than three millimeters. Replace the screw and repeat the measuring procedure. If less than nine cubes of fuel are poured out, then the soldering should be increased, if more, then reduced.
Step 3
Equally important is the refinement of the opening of the second chamber. Since its opening occurs due to the operation of the pneumatic drive, a delay occurs, which leads to a failure in operation. One option is to disassemble the pneumatic actuator and remove the spring, which causes the diaphragm to travel more freely, or leave the spring in place. Take a lead ball or pellet and plug it into the jet of the pneumatic drive of the second chamber. Next, using a drill, drill the first chamber jet about 2.5mm in diameter. With this method, dips are practically excluded in any ranges of engine operation.