A modern car is a combination of excellent aerodynamic qualities, an economical revving engine and a comfortable cabin in which the driver and his passengers feel completely safe. However, there is another important factor, without which the movement of any power-driven vehicle cannot be imagined even theoretically. These are reliable and efficient brakes, the correct operation of which is ensured by high-quality brake pads.
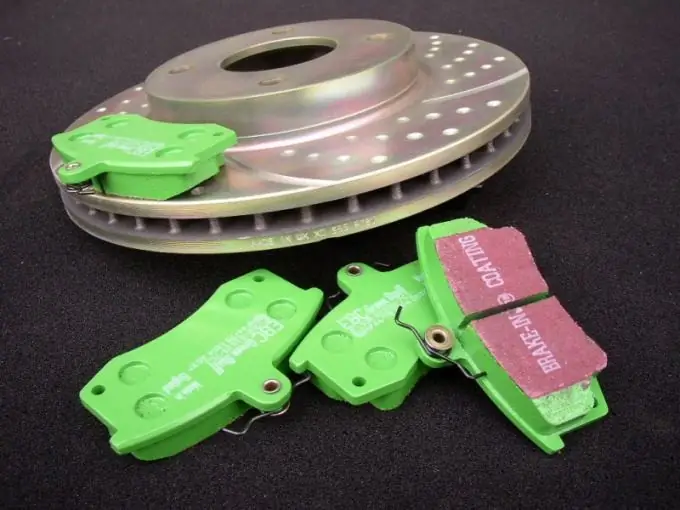
As you know, the faster a car goes, the longer its braking distance. The owners of famous car brands do their best so that the number of meters covered by the braking car depends only on the reaction of the driver himself. They constantly develop and improve the braking system, not forgetting, of course, about the brake pads, on the effective operation of which the lives of people largely depend.
The pads consist of a frame and friction pads. And if the frame as a structural part has not undergone significant modernization for a rather long period of time, then the linings, on the contrary, constantly change their composition and the percentage of chemical elements. Automotive companies that manufacture brake pads carefully hide the formulation and data on the chemical elements used in their products from competitors. And for engineers - developers of new technologies for the manufacture of friction linings, there are serious restrictions prescribed in the individual contract. In particular, they are prohibited from discussing or describing in any way the work process, as well as the finished products of the company, in order to exclude any possibility of leakage of information about the materials used in the manufacture of brake pads.
There is a division of the composition of the friction mixture into organic, asbestos and non-asbestos elements. It is largely arbitrary, since in fact the working mixture consists of more than 15 components. After combining these components in a certain proportion, the mixture is poured into special molds and pressed, first by cold, and then by hot method. The pressed part is ground and then undergoes quality control.
The reliability of the friction material as well as the clean sanding of the part is very important for driving safety. Huge forces and loads act on the pads during braking. After all, they work only due to the frictional force, literally wrapping around the brake disc and forcing it to stop. In this case, the strongest vibrations occur, and the surface temperature rises sharply, which cannot but affect the friction linings, which are simply erased. Therefore, one of the important characteristics of the lining material is reinforcement, which increases the resistance of the friction mixture to friction and high temperatures.